In the industrial field, thermal fluid systems have a wide range of applications, such as hydraulic systems, liquefied gas transmission and transportation systems, and HVAC systems. Most of these systems are complex and large. Once a local fault occurs, it is easy to cause very dangerous consequences, but it is not easy to detect. It is often necessary for experienced engineers to judge the size and location of the fault based on the monitoring results.
Quickly find faults, quickly locate fault locations, and accurately determine the severity of faults. These on-site emergency treatments have very high requirements on engineers' experience and business proficiency. Inevitably, there are problems such as poor reliability and high false positive rate.
In this regard, relevant research institutes have begun to use real-time synchronous simulation technology to solve the above problems in the filling process.
First, establish a one-dimensional system model of the filling system and complete the checking of the model. In the modeling process, it is necessary to directly input physical equations to customize special parts for commonly used media and components (such as liquefied gas, self-pressurized tank, vaporizer, etc.). For the flow resistance and heat transfer characteristics of each component in the system, the calibration of the existing experimental data ensures the accuracy of the model.
Based on the calibrated filling system model, it is possible to simulate different operating conditions and multiple fault responses. The simulation of the working conditions and faults can be done completely on a normal computer, which is more efficient and safer than the actual test. According to a large number of simulation results, summing up the rules, combined with the data accumulated in the actual work, the fault model library of the filling system can be established, and the system fault tree is formed for the fault process, which serves as the basis for subsequent fault diagnosis and zeroing.
At the actual filling site, the filling system model is directly run on the real-time simulator, and the simulation is performed in real time with the actual filling process. For the filling system model and the actual filling system, the same process instructions are sent synchronously, and key parameters in the system, such as pressure and temperature, are monitored in real time. If the actual process is carried out normally, it will be comparable to the real-time simulation result; once a certain fault occurs in the actual filling process, the key parameter values ​​after the link will deviate from the real-time simulation result, so that the fault can be directly judged. Location and so on. According to the degree of deviation between the two, combined with the existing engineering experience, the severity of the fault can be judged more accurately. Therefore, the engineer can quickly locate the fault location and efficiently troubleshoot the fault tree without affecting the normal operation of the test.
The real-time synchronous simulation model of the filling system is mainly composed of a filling system model, a real-time simulation system, a data processing and application database software, and a system integration device. Considering the versatility and convenience of model customization, the system model is performed by Dymola; due to the complexity of the system, in real-time simulation, the system model split runs in parallel on multiple cores of the ConCurrent simulator. The figure below shows the calibration of the flow data of a certain position in the pipeline in some processes, showing that the real-time synchronous simulation model can meet the accuracy requirements of offline fault simulation, real-time monitoring and comparison.
The real-time synchronous simulation system customized by Hengrun Technology for the filling system is mainly composed of Dymola filling system model, ConCurrent real-time parallel simulator, data processing and application database software, and system integration equipment. The figure below shows the calibration of the temperature data of a certain position of the conveying pipeline in some processes, showing that the real-time synchronous simulation model can meet the accuracy requirements of offline fault simulation, real-time monitoring and comparison.
For more information, please contact Hengrun Technology or send an email to
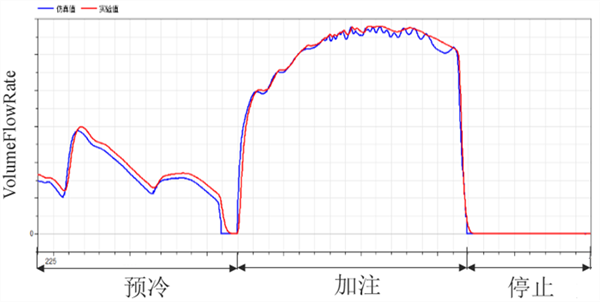
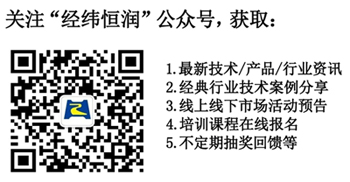
Slicer and dicer(meat dicer) are used in different fields of food industrial such as for meat, cheese, vegetables, fruits etc. Helper`s slicer and dicer seies are applied in both restaurant and industrial plant. To produce portioned bacon, the Rib chopper will help. To make vegatable and meat mixture for dumpling production, QD02 vegetable dicer will be the best choice.
In addition to them,we also supply the cubing machines.
Potato Slicer,Food Chopper,Vegetable Dicer,Vegetable Cutter,Meat Dicer,Cubing Machines
Helper Machinery Group Co., Ltd. , https://www.helperfoodtek.com